Fully integrated packing line meets pet food manufacturer’s automation and traceability needs
Endoline, working with Conveyor Systems Ltd, has created a customised end-of-line packing operation for GA Pet Food Partners – meeting space requirements and providing a long term automated solution which will enable the company to meet future demand.
As Europe’s leading manufacturer of own label premium dry pet foods, GA Pet Food Partners manufactures, packs and supplies pet food to some of the world’s leading pet food brands, exporting to over 50 countries worldwide.
Last year, the company invested over £80m into its Ingredients Kitchen as part of an ambitious expansion plan to develop a new dark store warehouse that will operate solely with robots and automation.
According to GA Pet Food Partners (GA), the automation of the entire process will provide its global network of partners confidence in the provenance and traceability of all recipes that are produced at the facility, while allowing for full traceability as every step is monitored.
Part of this commitment to automation included the packing process of the 80,000 tonnes of dry extruded pet food GA supplies each year.
Supplying four case erectors and its flagship 734 automatic random case sealer, Endoline worked with Conveyor Systems Ltd (CSL) to seamlessly connect each system together with conveyors to create an ergonomically friendly, automated line offering full reporting and traceability.
Modifications to meet the specification
In order to meet the wide case size range of GA, Endoline recommended the installation of two, 221 Case Erectors and two, 225 Case Erectors. While both systems are fully automatic, the 225 is designed to erect larger case sizes – up to 750mm open height. The 221 can erect up to 18 cases per minute, while the 225 runs at speeds of 10 cases per minute, providing GA Pet Food Partners with a potential case forming output of 56 cases per minute.
In addition, due to the weight variations of the filled pet food bags GA produces, between 5kg and 30kg, Endoline modified the case erectors to ensure that they were able to handle the heavy-duty cases used to hold each bag of pet food. To improve efficiency, Endoline engineers made mechanical changes to the empty case hopper on the erector to ensure the efficient and smooth delivery of cases down the hopper into the machine before erecting. The company’s unique dual opposing vacuum technology also ensures that each case is opened positively from both sides, and overcomes cases stuck together by glue migration which can happen during the case manufacturing process. The control systems on each case erector also allows for ease of case size changeover.
To maximise space efficiency, the case erectors were positioned at an angle to the line and CSL customised its conveyors to directly feed the packing line from each erector. “We designed four conveyor streams to work with each case erector. For these streams we used Interroll zero pressure, 24v accumulation roller conveyors to ensure the transportation of the cases without any risk of accumulation,” comments Jim Farquhar, Sales Director, Conveyor Systems Ltd.
A fully connected operation
Each formed case is labelled by an automatic labeller and read by a bar code reader to ensure that the size of the case corelates to the size of the pet food bag, safeguarding the smooth and efficient operation.
At the start of the line, bags full of pet food are decanted from a trolley onto an initial heavy duty plastic mattop belt conveyor, to take the loading impact, and inclined up using an incline belt conveyor. At the end of this process, a heavy duty plastic mattop conveyor was employed whereby the operator can remove the pet food bag for placement into the previously erected cartons.
Both the 24v zero pressure conveyors transporting the formed cases and the plastic mattop conveyors with bags of pet food run parallel to each other. As many of the cartons are tall, CSL customised the carton feeding conveyor to run on a decline before being transferred, reaching the packer for ergonomic packing.
The pack station, comprised of another heavy duty mattop conveyor mounted on top of a load cell, to allow the operator to confirm the weight of the packed order, which was reported back the GA’s WMS system.
Once filled, the case is transported on a 24v zero pressure conveyor, which was again customised by CSL to incorporate a reject conveyor which diverts a case off the main line if the bar code reader determines the size/weight of it to be incorrect.
Finally, a customised incline by CSL allowed the finished packed cases to run on an incline leading up into and through to the 734 for sealing.
Endoline’s 734 Fully Automatic Random Case Sealer has the ability to seal up to 22, random sized cases per minute. Again, the system was modified by Endoline to manage the slightly longer case size runs. The high speed, award winning system uses barcode scanning technology to recognise the cases dimensions prior to sealing which is how the sealer can achieve its high throughput.
“Through our automated systems and CSL’s experience in conveyor solutions we have created a packing line which is future-proof and able to deal with maximum output and case sizes,” comments Mark Budd, Sales Manager for Endoline Automation.
Endoline’s control systems have been interfaced with CSL’s mechanics and all of this is connected through software supplied by GA, creating a fully automated operation. “There is no room for error, and, through the software, GA can provide customers with full traceability and data reporting.” Mark comments.
Eventually, the entire packing line will be moved onto a concrete mezzanine floor within the GA warehouse. “It was vital that we created the line to fit within the required footprint. This is essentially a concept which both Endoline and CSL have proven to work well.” Mark concludes.
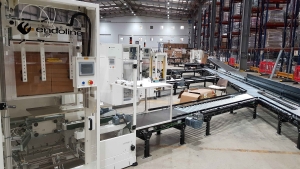
The entire line has been created to support GA Pet Food’s automation ambitions and the packing operation of 80,000 tonnes of dry extruded pet food
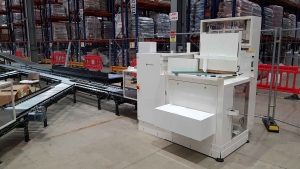
The Endoline Automation case erectors and CSL’s conveyor systems have been installed within a specific footprint so it is both ergonomically friendly, and can be later reinstated on a mezzanine floor